Previous | Next |
Yong Chen1, Kang Li2, and Xiaoping Qian3
1University of Southern California   2Illinois Institute of Technology   3University of Wisconsin-Madison  
Journal of Computing and Information Science in Engineering, 13(4), 2013
ASME International Design Engineering Technical Conferences &
Computers and Information in Engineering Conference (IDETC/CIE), 2012
IDETC 2012 Prakash Krishnaswami CAPPD Best Paper Award
Demo
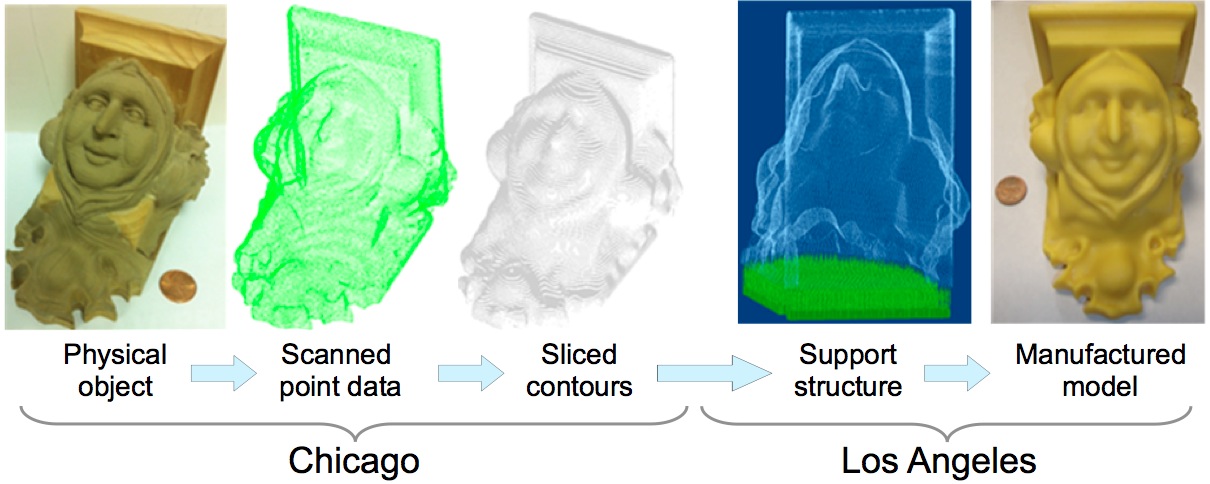

Abstract
This paper presents a new approach for tele-fabrication where a physical object is scanned in one location and fabricated in another location. This approach integrates three-dimensional (3D) scanning, geometric processing of scanned data, and additive manufacturing (AM) technologies. In this paper, we focus on a set of direct geometric processing techniques that enable the tele-fabrication. In this approach, 3D scan data are directly sliced into layer-wise contours. Sacrificial supports are generated directly from the contours and digital mask images of the objects and the supports for stereo-lithography apparatus (SLA) processes are then automatically generated. The salient feature of this approach is that it does not involve any intermediate geometric models such as STL, polygons, or nonuniform rational B-splines (NURBS) that are otherwise commonly used in prevalent approaches. The experimental results on a set of objects fabricated on several SLA machines confirm the effectiveness of the approach in faithfully tele-fabricating physical objects.